Discover What is Porosity in Welding and Its Impact on Structural Stability
The Scientific Research Behind Porosity: A Comprehensive Overview for Welders and Fabricators
Understanding the intricate mechanisms behind porosity in welding is essential for welders and producers aiming for impressive craftsmanship. As metalworkers delve right into the midsts of this sensation, they discover a world regulated by numerous variables that affect the development of these small voids within welds. From the composition of the base products to the details of the welding procedure itself, a wide variety of variables conspire to either worsen or ease the existence of porosity. In this extensive overview, we will certainly untangle the scientific research behind porosity, exploring its effects on weld quality and introduction progressed strategies for its control. Join us on this trip with the microcosm of welding imperfections, where accuracy fulfills understanding in the quest of flawless welds.
Recognizing Porosity in Welding
FIRST SENTENCE:
Examination of porosity in welding exposes crucial insights right into the honesty and high quality of the weld joint. Porosity, identified by the existence of cavities or spaces within the weld steel, is an usual worry in welding procedures. These gaps, if not correctly attended to, can compromise the architectural stability and mechanical homes of the weld, leading to possible failings in the finished item.

To find and measure porosity, non-destructive screening approaches such as ultrasonic screening or X-ray assessment are often utilized. These methods permit the identification of interior defects without jeopardizing the integrity of the weld. By evaluating the size, form, and distribution of porosity within a weld, welders can make enlightened choices to enhance their welding processes and accomplish sounder weld joints.
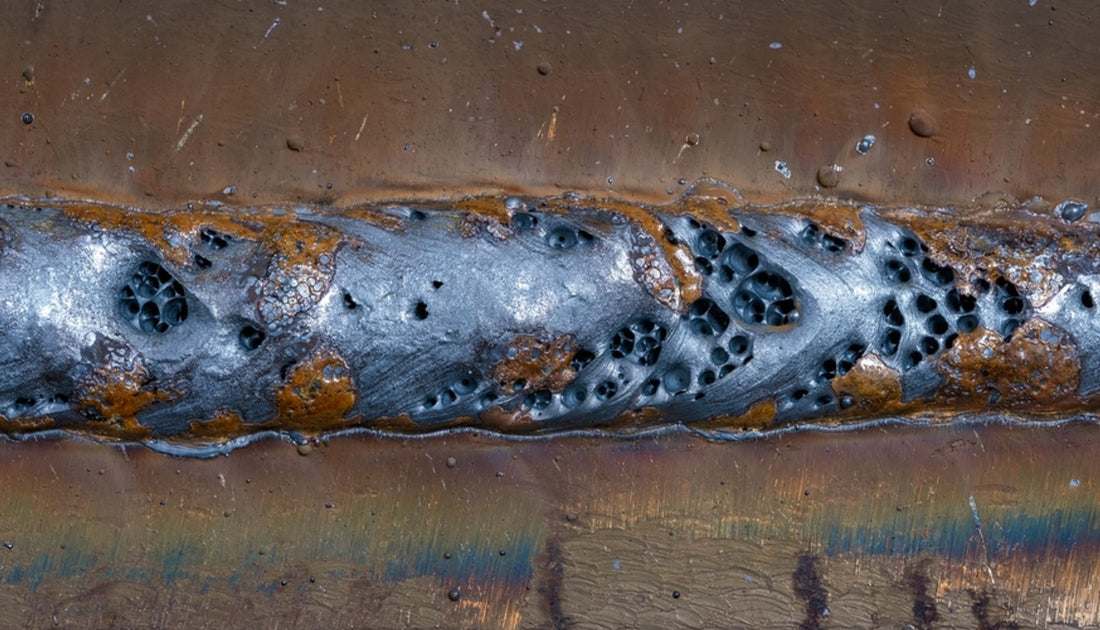
Factors Affecting Porosity Formation
The incident of porosity in welding is influenced by a myriad of aspects, varying from gas securing effectiveness to the ins and outs of welding parameter settings. One crucial variable adding to porosity development is poor gas shielding. When the securing gas, normally argon or carbon dioxide, is not effectively covering the weld pool, atmospheric gases like oxygen and nitrogen can infect the molten steel, resulting in porosity. In addition, the sanitation of the base products plays a considerable function. Contaminants such as rust, oil, or dampness can vaporize during welding, producing gas pockets within the weld. Welding parameters, including voltage, present, travel speed, and electrode type, additionally effect porosity formation. Using improper settings can create extreme spatter or warm input, which consequently can result in porosity. The welding technique employed, such as gas metal arc welding (GMAW) or protected metal arc welding (SMAW), can affect porosity formation due to variations in warm distribution and gas protection. Understanding and managing these elements are essential for reducing porosity in welding procedures.
Effects of Porosity on Weld Top Quality
Porosity formation dramatically compromises the architectural honesty and mechanical homes of bonded joints. When porosity exists in a weld, it creates spaces or dental caries within the material, decreasing the total stamina of the joint. These gaps work as anxiety focus points, making the weld more susceptible to breaking and failing under load. The existence of porosity likewise check this damages the weld's resistance to rust, as the trapped air or gases within the voids can react with the surrounding atmosphere, bring about destruction with time. In addition, porosity can hinder the weld's capability to withstand pressure or influence, further jeopardizing the total high quality and dependability of the bonded framework. In essential applications such as aerospace, auto, or structural buildings, where security and toughness are vital, the harmful impacts of porosity on weld high quality can have severe repercussions, highlighting the you can look here significance of lessening porosity through proper welding techniques and treatments.
Techniques to Lessen Porosity
Furthermore, making use of the suitable welding specifications, such as the appropriate voltage, present, and travel rate, is critical in avoiding porosity. Maintaining a consistent arc size and angle throughout welding additionally assists reduce the likelihood of porosity.

Additionally, choosing the appropriate securing gas and maintaining appropriate gas flow rates are essential in lessening porosity. Making use of the appropriate welding technique, such as back-stepping or using a weaving movement, can likewise assist disperse heat equally and decrease the chances of porosity formation. Making sure proper ventilation in the welding setting to get rid of any kind of potential resources of contamination is important for attaining porosity-free welds. By implementing these techniques, welders can efficiently decrease porosity and generate high-quality bonded joints.

Advanced Solutions for Porosity Control
Implementing cutting-edge modern technologies and innovative approaches plays a crucial duty in accomplishing remarkable control over porosity in welding processes. Additionally, utilizing sophisticated welding techniques such as pulsed MIG welding or customized environment welding can also help reduce porosity problems.
One more sophisticated service involves making use of sophisticated welding tools. For instance, utilizing equipment with built-in functions like waveform control and sophisticated power resources can improve weld high quality and lower porosity dangers. The application of automated welding systems with accurate control over specifications can dramatically minimize porosity flaws.
Furthermore, including advanced tracking and evaluation innovations such as official site real-time X-ray imaging or automated ultrasonic screening can help in discovering porosity early in the welding process, permitting immediate rehabilitative actions. Overall, integrating these innovative services can substantially improve porosity control and enhance the overall top quality of bonded parts.
Verdict
In conclusion, understanding the science behind porosity in welding is crucial for welders and makers to create top notch welds - What is Porosity. Advanced services for porosity control can better enhance the welding process and make certain a strong and reputable weld.